Table of contents
Needle roller bearings, aligning needle roller bearings
- Bearing design
- Load carrying capacity
- Compensation of angular misalignments
- Lubrication
- Sealing
- Speeds
- Noise
- Temperature range
- Cages
- Internal clearance
- Dimensions, tolerances
- Suffixes
- Structure of bearing designation
- Dimensioning
- Minimum load
- Design of bearing arrangements
- Mounting and dismounting
- Legal notice regarding data freshness
- Further information
Needle roller bearings
Needle roller bearings, aligning needle roller bearings
The bearings:
- can support high to very high radial forces
- are used when the load carrying capacity or accuracy of drawn cup needle roller bearings with open ends is no longer sufficient and the high load capacity of cylindrical roller bearings is not yet required
- can only support radial loads and, as a result, are highly suitable for use as non-locating bearings (they permit axial displacement of the shaft relative to the housing in the bearing)
- permit high speeds in spite of line contact
- compensate misalignments between the shaft and housing (aligning needle roller bearings)
- require only a very small radial design envelope, particularly if the bearing arrangement is designed without an inner ring
- are available in numerous sizes and designs
- result in particularly compact, cost-effective and economical bearing arrangements
Needle roller bearing in X-life quality: Cr = basic dynamic load rating |
![]() |
Bearing design
Design variants
Needle roller bearings are available as:
- needle roller bearings with ribs on the outer ring ➤ Figure to ➤ Figure
- needle roller bearings without ribs on the outer ring ➤ Figure and ➤ Figure
- aligning needle roller bearings ➤ Figure and ➤ Figure
- combined needle roller bearings ➤ link
Needle roller bearings are X-life bearings ➤ link.
In addition to the bearings described in this chapter, needle roller bearings are also available in other series, designs and sizes, as well as for specific applications, by agreement.
Needle roller bearings
Needle roller bearings are non-locating bearings
Needle roller bearings are rolling bearings with a low radial section height and high load carrying capacity, which are used as non-locating bearings and are part of the group of radial needle roller bearings. These bearings comprise machined outer rings, needle roller and cage assemblies and removable inner rings, i. e. they can be supplied with or without an inner ring in accordance with the application ➤ Figure to ➤ Figure. In contrast to the outer cups of drawn cup needle roller cups, which are produced by forming methods, the bearing rings are machined. Due to their non-locating bearing function, the bearings cannot guide the shaft axially in either direction.
Needle roller bearings with ribs on the outer ring
The needle roller and cage assembly is guided by the ribs
Needle roller bearings with ribs are ready-to-fit units. The outer ring and needle roller and cage assembly form a self-retaining unit. The needle roller and cage assembly is guided by the ribs on the outer ring. The outer ring has a lubrication groove and at least one lubrication hole. There is no relubrication facility in types NK with Fw ≦ 10 mm and NKI with d ≦ 7 mm. The bearings are predominantly of a single row design, type RNA69 is of a double row design above an enveloping circle diameter Fw = 40 mm and is therefore fitted with two needle roller and cage assemblies. The bearings are available:
- with or without an inner ring ➤ Figure and ➤ Figure
- in a single or double row design ➤ Figure and ➤ Figure
- as open or sealed versions ➤ Figure, ➤ Figure, ➤ section
Needle roller bearings with ribs on the outer ring, without inner ring
Available types
Needle roller bearings with ribs on the outer ring and without an inner ring are available in the following types and dimension series:
- NK, NKS, RNA48, RNA49, RNA69 (single row) ➤ Figure
- RNA69..-ZW (double row) ➤ Figure
- RNA49..-RSR, RNA49..-2RSR (sealed on one or both sides) ➤ Figure and ➤ section
For bearing arrangements with particularly compact radial dimensions
Bearings without an inner ring are highly suitable for bearing arrangements with particularly compact radial dimensions, if the shaft raceway can be hardened and ground ➤ section. If no inner ring is used, the shaft can be designed to a greater thickness and thus with increased rigidity.
Length compensation (axial displacement facility)
Radial needle roller bearings are used as non-locating bearings, i. e. when the shaft must allow axial length compensation relative to the housing. For bearings without an inner ring, the axial displacement facility of the shaft is dependent on the width of the shaft raceway.
Needle roller bearings with ribs on the outer ring, without inner ring, open Fr = radial load
|
![]() |
Needle roller bearings with ribs on the outer ring, without inner ring, sealed on one or both sides Fr = radial load
|
![]() |
Needle roller bearings with ribs on the outer ring, with inner ring
Available types
Needle roller bearings with ribs on the outer ring and with an inner ring are available in the following types and dimension series:
- NKI, NKIS, NA48, NA49, NA69 (single row) ➤ Figure
- NA69..-ZW (double row) ➤ Figure
- NA49..-RSR, NA49..-2RSR (sealed on one or both sides) ➤ Figure and ➤ section
Bearings with an inner ring are used if the shaft cannot be configured as a rolling bearing raceway. The bearings are of a single row design, NA69 is of a double row design from d ≧ 32 mm.
Axial displacement of the inner ring
For bearings with an inner ring, the axial displacement of the shaft relative to the housing occurs during rotational motion, without constraint in the bearing, between the needle rollers and the inner ring raceway without ribs. The maximum axial displacement s is given in the product tables. Where larger displacements occur, the standard ring can be replaced by a wider inner ring IR. Inner rings ➤ link.
Replacement of inner rings
In the case of the standard bearings, the inner rings are matched to the enveloping circle tolerance F6 and can be interchanged with each other (mixed use) within the same accuracy class.
Needle roller bearings with ribs on the outer ring, with inner ring, open Fr = radial load
|
![]() |
Needle roller bearings with ribs on the outer ring, with inner ring, sealed on one or both sides Fr = radial load
|
![]() |
Needle roller bearings without ribs on the outer ring
The bearing components can be mounted independently of each other
Needle roller bearings without ribs on the outer ring are ready-to-fit units. The bearings are not self-retaining. This means that the outer ring, needle roller and cage assembly and inner ring can be fitted independently of each other. The needle roller and cage assembly can be mounted in different ways: It can be fitted together with the shaft, the outer ring or the inner ring, or it can be subsequently inserted between the outer ring and shaft or inner ring. The needle roller and cage assembly and outer ring must not, however, be interchanged with identical components from other bearings during mounting, but should always be fitted as supplied. The majority of the bearings are of a single row design. Double row bearings comprise two single row needle roller and cage assemblies arranged adjacent to each other. They have a lubrication groove in the circumference of the outer ring, at least one lubrication hole in the outer ring and the suffix ZW-ASR1 ➤ section. Bearings are also available with a lubrication hole in the inner ring; these have the suffix IS1 ➤ section. Needle roller bearings without ribs on the outer ring are available:
- with and without an inner ring ➤ Figure and ➤ Figure
- in a single or double row design ➤ Figure and ➤ Figure
Needle roller bearings without ribs on the outer ring, without inner ring
Available types
Needle roller bearings without ribs on the outer ring and without an inner ring are available in the following types:
For bearing arrangements with particularly compact radial dimensions
Bearings without an inner ring are highly suitable for bearing arrangements with particularly compact radial dimensions, if the shaft raceway can be hardened and ground ➤ section. If no inner ring is used, the shaft can be designed to a greater thickness and thus with increased rigidity. If the shaft raceway is produced to the appropriate dimensional and geometrical accuracy, bearing arrangements with increased running accuracy can be achieved.
Length compensation (axial displacement facility)
Radial needle roller bearings are used as non-locating bearings, i. e. when the shaft must allow axial length compensation relative to the housing. For bearings without an inner ring, the axial displacement facility of the shaft is dependent on the width of the shaft raceway.
Needle roller bearings without ribs on the outer ring, without inner ring, open Fr = radial load
|
![]() |
Needle roller bearings without ribs on the outer ring, with inner ring
Available types
Needle roller bearings without ribs on the outer ring and with an inner ring are available in the following types:
Bearings with an inner ring are used if the shaft cannot be configured as a rolling bearing raceway.
Axial displacement of the inner ring
For bearings with an inner ring, the axial displacement of the shaft relative to the housing occurs during rotational motion, without constraint in the bearing, between the needle rollers and the inner ring raceway without ribs. The maximum axial displacement s is given in the product tables ➤ link. Where larger displacements occur, the standard ring can be replaced by a wider inner ring IR. Inner rings ➤ link.
Replacement of inner rings
The outer ring and the needle roller and cage assembly are matched to each other and must not be interchanged during mounting with components from other bearings of the same size. In the case of the standard bearings, the inner rings are matched to the enveloping circle tolerance F6 and can be interchanged with each other (mixed use) within the same accuracy class.
Needle roller bearings without ribs on the outer ring, with inner ring, open Fr = radial load
|
![]() |
Aligning needle roller bearings
Suitable for the compensation of angular misalignments
Aligning needle roller bearings comprise drawn outer cups, plastic support rings with a concave inner profile, outer rings with a spherical outside surface, needle roller and cage assemblies and removable inner rings ➤ Figure. As a result of their design, these bearings can compensate misalignments, since the outer ring, with its spherical outside surface, is able to move in the concave plastic support ring ➤ section. Due to their non-locating bearing function, the bearings can guide the shaft axially in either direction.
Aligning needle roller bearings without inner ring
Available types
Aligning needle roller bearings are available in type RPNA ➤ Figure.
For bearing arrangements with particularly compact radial dimensions
Bearings without an inner ring are highly suitable for bearing arrangements with low section height and particularly compact radial dimensions, if the shaft raceway can be hardened and ground ➤ section. If no inner ring is used, the shaft can be designed to a greater thickness and thus with increased rigidity.
Aligning needle roller bearing without inner ring Fr = radial load
|
![]() |
Aligning needle roller bearings with inner ring
Available types
Aligning needle roller bearings are available in type PNA ➤ Figure.
Bearings with an inner ring are used if the shaft cannot be configured as a rolling bearing raceway.
Axial displacement of the inner ring
For bearings with an inner ring, the axial displacement of the shaft relative to the housing occurs during rotational motion, without constraint in the bearing, between the needle rollers and the inner ring raceway without ribs. The maximum axial displacement s is given in the product tables ➤ link. Where larger displacements occur, the standard ring can be replaced by a wider inner ring. Inner rings ➤ link.
Replacement of inner rings
In the case of the standard bearings, the inner rings are matched to the enveloping circle tolerance F6 and can be interchanged with each other (mixed use) within the same accuracy class.
Aligning needle roller bearing with inner ring Fr = radial load |
![]() |
X-life premium quality
The radial needle roller bearings described here are X-life bearings. These bearings are characterised by a very high load carrying capacity and long rating life. This is achieved, for example, through the modified internal construction and optimised contact geometry between the needle rollers and raceways, as well as through the higher quality of the steel and rolling elements, higher surface quality and appropriate heat treatment and/or coating.
Advantages
Increased customer benefits due to X-life
The technical enhancements offer a range of advantages, such as:
- a more favourable load distribution in the bearing and thus a higher dynamic load carrying capacity of the bearings
- quieter running
- running with reduced friction and greater energy efficiency
- lower heat generation in the bearing
- higher possible speeds
- lower lubricant consumption and, consequently, longer maintenance intervals
- a measurably longer operating life
- high operational security
- compact, environmentally-friendly bearing arrangements
Lower operating costs, higher machine availability
In conclusion, these advantages improve the overall cost-efficiency of the bearing position significantly and thus bring about a sustainable increase in the efficiency of the machine and equipment.
Suffix XL
X-life radial needle roller bearings include the suffix XL in the designation ➤ Figure, ➤ Figure and ➤ link.
Calculated rating life and rating life verified in tests – comparison between X-life needle roller bearing and bearings without X-life quality Lnmr = adjusted reference rating life
|
![]() |
Areas of application
Wide application range
Due to their special technical features, X-life needle roller bearings are highly suitable for bearing arrangements in:
- printing machinery
- the food and packaging industry
- compressors
- fluid and hydraulic pumps
- automotive chassis and gearboxes
- gearboxes for industrial, rail and wind turbine applications
- agricultural vehicles and equipment
X-life indicates a high product performance density and thus a particularly significant benefit to the customer.
Load carrying capacity
The bearings are pure radial bearings
Radial needle roller bearings support very high radial forces due to the presence of line contact, but may only be subjected to purely radial load. If the bearing position is also required to support axial forces, the needle roller bearings can, for example, be combined with axial needle roller bearings AXW ➤ Figure. An extensive range of combined needle roller bearings is also available for combined loads ➤ link.
If the surface of the shaft raceway is produced to DIN 617, the basic load ratings Cr in the product tables must be reduced by 15%.
Radial needle roller bearing combined with axial needle roller bearing Fr = radial load Fa = axial load
|
![]() |
Compensation of angular misalignments
The bearings are not suitable for the compensation of shaft misalignments relative to the housing
Needle roller bearings with or without ribs are not suitable for the compensation of angular misalignments. The extent to which a misalignment of the shaft can be tolerated relative to the housing bore is dependent on factors such as the design of the bearing arrangement, the size of the bearing, the operating clearance and the load. As a result, no guide value can be specified here for a possible misalignment. If angular misalignments occur, aligning needle roller bearings can be used ➤ Figure.
In all cases, misalignments cause increased running noise, place in-creased strain on the cages and have a harmful influence on the operating life of the bearings.
Aligning needle roller bearings
Aligning needle roller bearings can compensate static misalignment
Due to the spherical outer ring and the concave support ring, aligning bearings can compensate static misalignments between the shaft and housing of up to 3° ➤ Figure and ➤ section. The bearings must not, however, be used to support swivel or tumbling motion. During adjustment motion between the outer cup and the ring, a breakaway torque occurs. In order that adjustment motion can take place, the tolerances for the housing bore must be observed ➤ Table.
Compensation of misalignments
|
![]() |
Lubrication
Needle roller bearings with or without ribs on the outer ring
Greased bearings
The sealed bearings are greased with a high quality lithium complex soap grease to GA08. Arcanol Load150 is suitable for relubrication. For this purpose, the outer ring has a lubrication groove and a lubrication hole ➤ section.
Do not wash greased bearings out prior to mounting. If mounting is carried out using thermal tools, the bearings should not be heated to a temperature in excess of +80 °C, taking account of the grease filling and seal material. If higher heating temperatures are required, it must be ensured that the permissible upper temperature limits for grease and seals are not exceeded. Schaeffler recommends the use of induction heating devices for heating purposes ➤ link.
Ungreased bearings
Open bearings are not greased. They must be lubricated with oil or grease.
Compatibility with plastic cages
When using bearings with plastic cages, compatibility between the lubricant and the cage material must be ensured if synthetic oils, lubricating greases with a synthetic oil base or lubricants containing a high proportion of EP additives are used.
Observe oil change intervals
Aged oil and additives in the oil can impair the operating life of plastics at high temperatures. As a result, stipulated oil change intervals must be strictly observed.
If there is any uncertainty regarding the suitability of the selected lubricant for the application, please consult Schaeffler or the lubricant manufacturer.
Sealing
The bearings are open or sealed
Needle roller bearings are available in an unsealed design in accordance with DIN 617:2008 and ISO 3245:2015 and a sealed design in accordance with DIN 617:2008.
Sealed bearings
Integrated seals are particularly space-saving
Under normal operating conditions, contact seals give protection against contamination, spray water and the loss of lubricant. The integration of such seals into the bearing provides a compact, reliable, proven and economical sealing solution ➤ Figure and ➤ Figure. The sealing material used is the oil-resistant and wear-resistant elastomer material NBR. The seal lips are in contact with a defined contact pressure against the sliding surface.
Unsealed bearings
Providing seal in the adjacent construction
In the case of unsealed bearings, sealing of the bearing position must be carried out in the adjacent construction. This must reliably prevent:
- moisture and contaminants from entering the bearing
- the egress of lubricant from the bearing
Sealing rings must not be used as running surfaces for the cage, as these will be damaged as a result and no longer able to fulfil their sealing function.
Sealing of the bearing position with a sealing ring G
Effective sealing elements for use in sealing open bearings
Bearing positions with open needle roller bearings can be sealed cost-effectively with sealing rings G. The sealing rings are designed as contact seals and are arranged in front of the bearing ➤ Figure. They are suitable for circumferential velocities at the running surface of up to 10 m/s and protect the bearing position reliably against contamination, spray water and the loss of lubricant. The sealing rings are matched to the low radial dimensions of needle roller bearings. They are very easy to fit, since they are simply pressed into the housing bore.
Sealing of the bearing position with a sealing ring G
|
![]() |
Speeds
Limiting speeds and speed ratings in the product tables
The product tables generally give two speeds for the bearings ➤ link:
- the kinematic limiting speed nG
- the thermal speed rating nϑr
Limiting speeds
The limiting speed nG is the kinematically permissible speed of the bearing. Even under favourable mounting and operating conditions, this value should not be exceeded without prior consultation with Schaeffler ➤ link.
The values given in the product tables are valid for oil lubrication in the case of bearings without seals and for grease lubrication where bearings are supplied greased and with seals.
Values for grease lubrication
For grease lubrication, 60% of the value stated in the product tables is permissible in the case of aligning needle roller bearings.
Reference speeds
nϑr is used to calculate nϑ
The thermal speed rating nϑr is not an application-oriented speed limit, but is a calculated ancillary value for determining the thermally safe operating speed nϑ ➤ link.
Bearings with contact seals
For bearings with contact seals, no speed ratings are defined in accordance with DIN ISO 15312:2004. As a result, only the limiting speed nG is given in the product tables for these bearings.
Noise
Schaeffler Noise Index
The Schaeffler Noise Index (SGI) is not yet available for this bearing type ➤ link. The data for these bearing series will be introduced and updated in stages.
Temperature range
Limiting values
The operating temperature of the bearings is limited by:
- the dimensional stability of the bearing rings and rolling elements
- the cage
- the lubricant
- the seals
Possible operating temperatures of needle roller bearings with ribs ➤ Table.
Permissible temperature ranges
Operating temperature |
Needle roller bearings with or without ribs, |
||
---|---|---|---|
open bearings |
sealed bearings, |
with plastic cage |
|
|
–30 °C to +120 °C |
–20 °C to +100 °C limited by the lubricant, seal material and |
–20 °C to +120 °C |
In the event of anticipated temperatures which lie outside the stated values, please contact Schaeffler.
Cages
Solid cages made from polyamide PA66 and sheet steel are used as standard
The standard cages are made from sheet steel or plastic (polyamide PA66). Bearings with a plastic cage have the suffix TV. Aligning needle roller bearings are fitted with sheet steel cages.
Internal clearance
Radial internal clearance
The standard is CN
Needle roller bearings with inner ring are manufactured as standard with radial internal clearance CN (normal) ➤ Table. CN is not stated in the designation.
For bearings with ribs on the outer ring, certain sizes are also available by agreement with the larger internal clearance C3.
The values for radial internal clearance in bearings with an inner ring correspond to DIN 620-4:2004 (ISO 5753-1:2009) ➤ Table. These are valid for bearings which are free from load and measurement forces (without elastic deformation).
Bearings with inner ring
Radial internal clearance of needle roller bearings with inner ring
Nominal bore diameter |
Radial internal clearance |
||||
---|---|---|---|---|---|
d |
CN |
C3 |
|||
mm |
μm |
μm |
|||
over |
incl. |
min. |
max. |
min. |
max. |
‒ |
24 |
20 |
45 |
35 |
60 |
24 |
30 |
20 |
45 |
35 |
60 |
30 |
40 |
25 |
50 |
45 |
70 |
40 |
50 |
30 |
60 |
50 |
80 |
50 |
65 |
40 |
70 |
60 |
90 |
65 |
80 |
40 |
75 |
65 |
100 |
80 |
100 |
50 |
85 |
75 |
110 |
100 |
120 |
50 |
90 |
85 |
125 |
120 |
140 |
60 |
105 |
100 |
145 |
continued ▼ |
Radial internal clearance of needle roller bearings with inner ring
Nominal bore diameter |
Radial internal clearance |
||||
---|---|---|---|---|---|
d |
CN |
C3 |
|||
mm |
μm |
μm |
|||
over |
incl. |
min. |
max. |
min. |
max. |
140 |
160 |
70 |
120 |
115 |
165 |
160 |
180 |
75 |
125 |
120 |
170 |
180 |
200 |
90 |
145 |
140 |
195 |
200 |
225 |
105 |
165 |
160 |
220 |
225 |
250 |
110 |
175 |
170 |
235 |
250 |
280 |
125 |
195 |
190 |
260 |
280 |
315 |
130 |
205 |
200 |
275 |
315 |
355 |
145 |
225 |
225 |
305 |
355 |
400 |
190 |
280 |
280 |
370 |
400 |
450 |
210 |
310 |
310 |
410 |
450 |
500 |
220 |
330 |
330 |
440 |
continued ▲ |
Enveloping circle diameter Fw for bearings without an inner ring
In the case of bearings without an inner ring, the enveloping circle diameter is used
In the case of bearings without inner ring, the enveloping circle dimension Fw is used instead of the radial internal clearance. The enveloping circle is the inner inscribed circle of the needle rollers in clearance-free contact with the outer raceway. For bearings before fitting, the enveloping circle Fw is in the tolerance class F6. Deviations ➤ Table.
Deviations for the enveloping circle diameter
Enveloping |
Tolerance class F6 |
Tolerance class F8 |
|||
---|---|---|---|---|---|
mm |
Tolerance for enveloping circle diameter Fw |
||||
upper deviation |
lower deviation |
upper deviation |
lower deviation |
||
over |
incl. |
μm |
μm |
μm |
μm |
3 |
6 |
+18 |
+10 |
+28 |
+10 |
6 |
10 |
+22 |
+13 |
+35 |
+13 |
10 |
18 |
+27 |
+16 |
+43 |
+16 |
18 |
30 |
+33 |
+20 |
+53 |
+20 |
30 |
50 |
+41 |
+25 |
+64 |
+25 |
50 |
80 |
+49 |
+30 |
+76 |
+30 |
80 |
120 |
+58 |
+36 |
+90 |
+36 |
120 |
180 |
+68 |
+43 |
+106 |
+43 |
180 |
250 |
+79 |
+50 |
+122 |
+50 |
250 |
315 |
+88 |
+56 |
+137 |
+56 |
315 |
400 |
+98 |
+62 |
+151 |
+62 |
400 |
500 |
+108 |
+68 |
+165 |
+68 |
Bearings without ribs on the outer ring
If the enveloping circle is to be in tolerance class F6, the outer ring/ needle roller cage assembly as a matched pair (as delivered) must not be interchanged with parts from other matched pairs.
Dimensions, tolerances
Dimension standards
The main dimensions of needle roller bearings correspond to ISO 15:2017. The main dimensions of types RNA48, NA48, RNA49, NA49, RNA69, NA69 correspond to DIN 617:2008 and ISO 1206:2001.
Nominal dimensions of needle roller bearings with ribs ➤ link.
Chamfer dimensions
The limiting dimensions for chamfer dimensions correspond to DIN 620‑6:2004. The maximum chamfer dimensions for the inner rings to DIN 620-6:2004 must be taken into consideration. Overview and limiting values ➤ section. Nominal value of chamfer dimension ➤ link.
Tolerances
The tolerances for the dimensional and running accuracy of needle roller bearings correspond to ISO 492:2014. This excludes the types RNA48, NA48, RNA49, NA49, RNA69, NA69and aligning needle roller bearings; the dimensional and running tolerances of these bearings correspond to ISO 1206:2001. Needle roller bearings with ribs are available by agreement with increased dimensional, geometrical and running accuracy (suffix P5). This excludes the outside diameter and the width of the outer cup in aligning needle roller bearings. The width has a tolerance of ±0,5 mm.
Suffixes
For a description of the suffixes used in this chapter ➤ Table and medias interchange http://www.schaeffler.de/std/1B69.
Suffixes and corresponding descriptions
Suffix |
Description of suffix |
|
---|---|---|
ASR1 |
Lubrication hole and lubrication groove in the outer ring, dependent on the size |
Standard |
C3 |
Radial internal clearance C3 (larger than normal) |
Special design, |
D |
Bearing with improved steel cage for downsizing option |
Standard |
IS1 |
Lubrication hole in the inner ring, dependent |
Standard |
P5 |
Bearing with high dimensional, geometrical and running accuracy |
Special design, |
RSR |
Contact seal on one side (lip seal) |
Standard |
TV |
Bearing with cage made from glass fibre reinforced polyamide PA66 |
Standard |
TW |
Bearing with cage made from glass fibre reinforced polyamide PA66 and two short needle rollers per cage pocket |
Available by agreement |
XL |
X-life bearing |
Standard |
ZW |
Double row design, dependent on the size |
Standard |
2RSR |
Contact seal on both sides (lip seal) |
Standard |
Structure of bearing designation
Examples of composition of bearing designation
The designation of bearings follows a set model. Examples ➤ Figure to ➤ Figure. The composition of designations is subject in part to DIN 623-1 ➤ Figure.
Single row needle roller bearing with ribs on the outer ring, without inner ring, open: designation structure |
![]() |
Single row needle roller bearing with ribs on the outer ring, without inner ring, sealed on both sides: designation structure |
![]() |
Double row needle roller bearing without ribs on the outer ring, without inner ring, open: designation structure |
![]() |
Aligning needle roller bearing with inner ring: designation structure |
![]() |
Dimensioning
Equivalent dynamic bearing load
P = Fr under purely radial load of constant magnitude and direction
The basic rating life equation L = (Cr/P)p used in the dimensioning of bearings under dynamic load assumes a load of constant magnitude and direction. In radial bearings, this is purely radial load Fr. If this condition is met, the bearing load Fr is used in the rating life equation for P (P = Fr) ➤ Equation.
Needle roller bearings and aligning needle roller bearings are non-locating bearings and may only be subjected to radial load.
Equivalent dynamic load
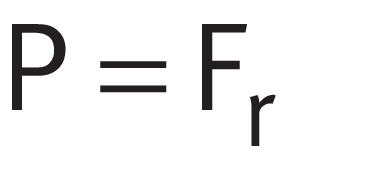
Legend
P | N |
Equivalent dynamic bearing load |
Fr | N |
Radial load |
Equivalent static bearing load
For needle roller bearings subjected to static load ➤ Equation.
Equivalent static load
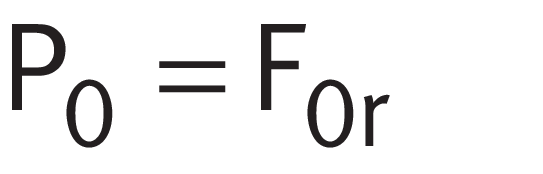
Legend
P0 | N |
Equivalent static bearing load |
F0r | N |
Largest radial load present (maximum load) |
Static load safety factor
S0 = C0/P0
In addition to the basic rating life L (L10h), it is also always necessary to check the static load safety factor S0 ➤ Equation.
Static load safety factor
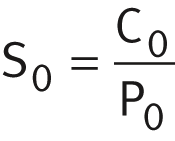
Legend
S0 | - |
Static load safety factor |
C0 | N |
Basic static load rating |
P0 | N |
Equivalent static bearing load |
Minimum load
In order to prevent damage due to slippage, a minimum radial load of P > C0r/60 is required
In order that no slippage occurs between the contact partners, the needle roller bearings must be constantly subjected to a sufficiently high load. Based on experience, a minimum radial load of the order of P > C0r/60 is thus necessary. In most cases, however, the radial load is already higher than the requisite minimum load due to the weight of the supported parts and the external forces.
If the minimum radial load is lower than indicated above, please consult Schaeffler.
Design of bearing arrangements
Support bearing rings over their entire circumference and width
In order to allow full utilisation of the load carrying capacity of the bearings and thus also achieve the requisite rating life, the bearing rings must be rigidly and uniformly supported by means of contact surfaces over their entire circumference and over the entire width of the raceway. Support can be provided by means of a cylindrical seating surface. The seating and contact surfaces should not be interrupted by grooves, holes or other recesses. The accuracy of mating parts must meet specific requirements ➤ Table to ➤ Table.
Radial location
For secure radial location, tight fits are necessary
Needle roller bearings with an inner ring are radially located by means of fits on the shaft and in the housing. In addition to supporting the rings adequately, the bearings must also be securely located in a radial direction, to prevent creep of the bearing rings on the mating parts under load. This is generally achieved by means of tight fits between the bearing rings and the mating parts. If the rings are not secured adequately or correctly, this can cause severe damage to the bearings and adjacent machine parts. Influencing factors, such as the conditions of rotation, magnitude of the load, internal clearance, temperature conditions, design of the mating parts, mounting and dismounting options etc., must be taken into consideration in the selection of fits.
If shock type loads occur, tight fits (transition fit or interference fit) are required to prevent the rings from coming loose at any point. Clearance, transition or interference fits ➤ Table and ➤ Table.
The following information provided in Technical principles must be taken into consideration in the design of bearing arrangements:
- conditions of rotation ➤ link
- tolerance classes for cylindrical shaft seats (radial bearings) ➤ Table
- shaft fits ➤ Table
- tolerance classes for bearing seats in housings (radial bearings) ➤ Table
- housing fits ➤ Table
Axial location – location methods
The bearings must also be securely located in an axial direction
As a tight fit alone is not normally sufficient to also locate the bearing rings securely on the shaft and in the housing bore in an axial direction, this must usually be achieved by means of an additional axial location or retention method. The axial location of the bearing rings must be matched to the type of bearing arrangement. Shaft and housing shoulders, housing covers, nuts, spacer rings and retaining rings etc., are fundamentally suitable ➤ Figure and ➤ Figure.
Axial location of the bearing rings in bearings with ribs on the outer ring
|
![]() |
Axial location of the bearing rings in bearings without ribs on the outer ring
|
![]() |
Axial guidance of the needle roller and cage assemblies in bearings without ribs on the outer ring
The needle roller and cage assemblies must be axially guided on lateral, burr-free running surfaces. The running surfaces for the cage must be precision machined (Ra 2) and resistant to wear. The product tables give the maximum value of the radius ra, the diameters of the abutment shoulders da, Da and the dimension db, Db for axial guidance of the needle roller and cage assembly. Mounting dimensions ➤ link.
Tolerances of the housing bore for aligning needle roller bearings
Tolerance classes and surface design for housings, as a function of the material – for aligning needle roller bearings
Housing material |
Bore tolerance |
Roundness tolerance |
Parallelism tolerance |
Recommended mean roughness value |
---|---|---|---|---|
Ramax (Rzmax) |
||||
max. |
max. |
μm |
||
Steel or cast iron |
N6 Ⓔ |
IT5/2 |
IT5/2 |
0,8 (4) |
Light metal |
R6 Ⓔ |
IT5/2 | IT5/2 | 0,8 (4) |
Dimensional, geometrical and running accuracy of cylindrical bearing seats
A minimum of IT6 should be provided for the shaft seat and a minimum of IT7 for the housing seat
The accuracy of the cylindrical bearing seat on the shaft and in the housing should correspond to the accuracy of the bearing used. For needle roller bearings with ribs with the tolerance class Normal, the shaft seat should correspond to a minimum of standard tolerance grade IT6 and the housing seat to a minimum of IT7. Guide values for the geometrical and positional tolerances of the bearing seating surfaces ➤ Table, tolerances t1 to t3 in accordance with ➤ Figure. Numerical values for IT grades ➤ Table.
Guide values for the geometrical and positional tolerances of bearing seating surfaces
Bearing |
Bearing seating surface |
Standard tolerance grades to ISO 286-1 |
||||
---|---|---|---|---|---|---|
to ISO 492 |
to DIN 620 |
Diameter tolerance |
Roundness tolerance |
Parallelism tolerance |
Total axial runout |
|
t1 |
t2 |
t3 |
||||
Normal |
PN (P0) |
Shaft |
IT6 (IT5) |
Circumferential load IT4/2 |
Circumferential load IT4/2 |
IT4 |
Shaft | IT6 (IT5) |
Point load IT5/2 |
Point load IT5/2 |
IT4 | ||
Housing |
IT7 (IT6) |
Circumferential load IT5/2 |
Circumferential load IT5/2 |
IT5 |
||
Housing | IT7 (IT6) |
Point load IT6/2 |
Point load IT6/2 |
IT5 | ||
‒ |
P5 |
Shaft |
IT5 |
Circumferential load IT2/2 |
Circumferential load IT2/2 |
IT2 |
Shaft | IT5 |
Point load IT3/2 |
Point load IT3/2 |
IT2 | ||
Housing |
IT6 |
Circumferential load IT3/2 |
Circumferential load IT3/2 |
IT3 |
||
Housing | IT6 |
Point load IT4/2 |
Point load IT4/2 |
IT3 |
Numerical values for ISO standard tolerances (IT grades) to ISO 286-1:2010
IT grade |
Nominal dimension in mm |
||||||||||||
---|---|---|---|---|---|---|---|---|---|---|---|---|---|
over |
3 |
6 |
10 |
18 |
30 |
50 |
80 |
120 |
180 |
250 |
315 |
400 |
|
incl. |
6 |
10 |
18 |
30 |
50 |
80 |
120 |
180 |
250 |
315 |
400 |
500 |
|
Values in μm |
|||||||||||||
IT2 |
1,5 |
1,5 |
2 |
2,5 |
2,5 |
3 |
4 |
5 |
7 |
8 |
9 |
10 |
|
IT3 |
2,5 |
2,5 |
3 |
4 |
4 |
5 |
6 |
8 |
10 |
12 |
13 |
15 |
|
IT4 |
4 |
4 |
5 |
6 |
7 |
8 |
10 |
12 |
14 |
16 |
18 |
20 |
|
IT5 |
5 |
6 |
8 |
9 |
11 |
13 |
15 |
18 |
20 |
23 |
25 |
27 |
|
IT6 |
8 |
9 |
11 |
13 |
16 |
19 |
22 |
25 |
29 |
32 |
36 |
40 |
|
IT7 |
12 |
15 |
18 |
21 |
25 |
30 |
35 |
40 |
46 |
52 |
57 |
63 |
Roughness of cylindrical bearing seating surfaces
Ra must not be too high
The roughness of the bearing seats must be matched to the tolerance class of the bearings. The mean roughness value Ra must not be too high, in order to maintain the interference loss within limits. The shafts must be ground, while the bores must be precision turned. Guide values as a function of the IT grade of bearing seating surfaces ➤ Table.
Roughness values for cylindrical bearing seating surfaces – guide values
Nominal diameter d (D) |
Recommended mean roughness value Ramax |
||||
---|---|---|---|---|---|
mm |
μm |
||||
Diameter tolerance (IT grade) |
|||||
over |
incl. |
IT7 |
IT6 |
IT5 |
IT4 |
‒ |
80 |
1,6 |
0,8 |
0,4 |
0,2 |
80 |
500 |
1,6 |
1,6 |
0,8 |
0,4 |
Mounting dimensions
The contact surfaces for the rings must be of sufficient height
The mounting dimensions of the shaft and housing shoulders, and spacer rings etc., must ensure that the contact surfaces for the bearing rings are of sufficient height. However, they must also reliably prevent rotating parts of the bearing from grazing stationary parts. The abutment shoulders (shaft, housing) should be perpendicular to the bearing axis.
The transition from the bearing seat to the abutment shoulder must be designed with rounding to DIN 5418 or an undercut to DIN 509.
Chamfer dimensions
The chamfer dimensions r are given in the product tables. These dimensions are limiting dimensions (minimum dimensions); the actual values should not be lower than specified. The overlap between the snap rings and the end faces of the bearing rings must be sufficiently large.
Raceway for bearings without an inner ring (direct bearing arrangement)
The raceway must be suitable as a rolling bearing raceway
In the case of needle roller bearings without an inner ring, the rolling element raceway on the shaft must be hardened and ground. Tolerances and surface designs are shown in ➤ Table. The surface hardness of the raceway must be 670 HV to 840 HV, the hardening depth CHD or SHD must be sufficiently large.
The values in the tables are valid for housing tolerances up to K7 Ⓔ. For tighter housing bores, the operating clearance should be checked by either calculation or measurement.
Tolerance classes and surface design of raceways for needle roller bearings without an inner ring
Shaft |
Shaft |
Design of raceway |
|||||
---|---|---|---|---|---|---|---|
Roundness tolerance |
Parallelism tolerance |
Recommended mean roughness value |
|||||
Nominal dimension |
Operating clearance |
Ramax (Rzmax) |
|||||
mm |
|||||||
over |
incl. |
small |
normal |
large |
max. |
max. |
μm |
‒ |
65 |
k5 |
h5 |
g6 |
IT3 |
IT3 |
0,1 (0,4) |
65 |
80 |
k5 |
h5 |
f6 |
IT3 | IT3 | 0,1 (0,4) |
80 |
120 |
k5 |
g5 |
f6 |
IT3 | IT3 |
0,15 (0,63) |
120 |
160 |
k5 |
g5 |
f6 |
IT3 | IT3 |
0,2 (1) |
160 |
180 |
k5 |
g5 |
e6 |
IT3 | IT3 | 0,2 (1) |
180 |
200 |
j5 |
g5 |
e6 |
IT3 | IT3 | 0,2 (1) |
200 |
250 |
j5 |
f6 |
e6 |
IT3 | IT3 | 0,2 (1) |
250 |
315 |
h5 |
f6 |
e6 |
IT3 | IT3 | 0,2 (1) |
315 |
415 |
g5 |
f6 |
d6 |
IT3 | IT3 | 0,2 (1) |
- The envelope requirement Ⓔ applies.
Shaft raceway to DIN 617
If the surface of the shaft raceway is produced to DIN 617, the basic load ratings Cr in the product tables must be reduced by 15% ➤ section.
Steels for the raceway
Through hardening steels
Through hardening steels in accordance with ISO 683-17 (e. g. 100Cr6) are suitable as materials for rolling bearing raceways in direct bearing arrangements. These steels can also be surface layer hardened.
Case hardening steels
Case hardening steels must correspond to DIN EN ISO 683-17 (e. g. 17MnCr5, 18CrNiMo7-6) or EN 10084 (e. g. 16MnCr5).
Steels for inductive surface layer hardening
For flame and induction hardening, steels in accordance with DIN EN ISO 683-17 (e. g. C56E2, 43CrMo4) or DIN 17212 (e. g. Cf53) should be used.
Raceway hardness of less than 670 HV
If the raceway fulfils the requirements for rolling bearing materials but the raceway hardness is less than 670 HV, the load on the bearing arrangement cannot be as high as the full load carrying capacity of the bearing. In order to determine the dynamic and static load carrying capacity of the bearing arrangement, the basic dynamic load rating C of the bearings must be multiplied by the reduction factor H (dynamic hardness factor) and the basic static load rating C0r by the reduction factor fH0 (static hardness factor) ➤ Figure and ➤ Figure.
Dynamic hardness factor at reduced hardness of raceways/rolling elements fH = dynamic hardness factor HV, HRC = surface hardness |
![]() |
Static hardness factor at reduced hardness of raceways/rolling elements fH0 = static hardness factor HV, HRC = surface hardness |
![]() |
Determining the case hardening depth
Approximation value for case hardening depth
An approximation value for determining the minimum hardness depth is given in ➤ Equation. The reference value for the load present is the equivalent stress in accordance with the distortion energy hypothesis (DEH) as a function of the rolling element diameter Dw and the magnitude of the load.
Case hardening depth

Legend
CHD | mm |
Case hardening depth |
Dw | mm |
Rolling element diameter |
The local hardness must always be above the local requisite hardness, which can be calculated from the equivalent stress.
Determining the surface hardening depth
In these surface hardening methods, the load and contact geometry must be taken into consideration when determining the requisite hardening depth.
For calculation of the surface hardening depth SHD ➤ Equation.
Surface hardening depth

Legend
SHD | mm |
Surface hardening depth |
Dw | mm |
Rolling element diameter |
Rp0,2 | N/mm2 |
Yield point of base material |
Mounting and dismounting
The mounting and dismounting options for needle roller bearings with ribs, by thermal, hydraulic or mechanical methods, must be taken into consideration in the design of the bearing position.
Aligning needle roller bearings
Mounting using pressing mandrel
Due to the drawn outer cup, the bearings must be mounted using a special pressing mandrel ➤ link. The marked side of the bearing should be in contact with the flange of the mandrel. A toroidal ring on the mandrel holds the bearing securely on the mandrel.
Schaeffler Mounting Handbook
Rolling bearings must be handled with great care
Rolling bearings are well-proven precision machine elements for the design of economical and reliable bearing arrangements, which offer high operational security. In order that these products can function correctly and achieve the envisaged operating life without detrimental effect, they must be handled with care.
The Schaeffler Mounting Handbook MH 1 gives comprehensive information about the correct storage, mounting, dismounting and maintenance of rotary rolling bearings http://www.schaeffler.de/std/1B68. It also provides information which should be observed by the designer, in relation to the mounting, dismounting and maintenance of bearings, in the original design of the bearing position. This book is available from Schaeffler on request.
Legal notice regarding data freshness
The further development of products may also result in technical changes to catalogue products
Of central interest to Schaeffler is the further development and optimisation of its products and the satisfaction of its customers. In order that you, as the customer, can keep yourself optimally informed about the progress that is being made here and with regard to the current technical status of the products, we publish any product changes which differ from the printed version in our electronic product catalogue.
We therefore reserve the right to make changes to the data and illustrations in this catalogue. This catalogue reflects the status at the time of printing. More recent publications released by us (as printed or digital media) will automatically precede this catalogue if they involve the same subject. Therefore, please always use our electronic product catalogue to check whether more up-to-date information or modification notices exist for your desired product.
Further information
In addition to the data in this chapter, the following chapters in Technical principles must also be observed in the design of bearing arrangements: